Fruit Fly Flight Behavior Characterization Using MEMS Force Sensors
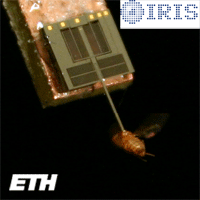
The fruit fly (Drosophila melanogaster), shown in Figure 1, is a model organism studied by biologists for almost a century, and possesses a highly developed flight control system that provides the insect with the capability to perform robust stable flight, as well as exceedingly rapid and precise turning maneuvers. The neurophysiology and biomechanics are inextricably linked and must be considered at the systems level. Multimodal sensory input converges on only 18 control muscles [1] that are responsible for the fine-tuning of wing motion for maneuvering, the aerodynamic basis of which has recently been revealed [2]. Beyond its impressive flight behavior, the fact that Drosophila melanogaster is completely autonomous, extremely small, highly robust, and self replicating makes this organism particularly interesting from a microrobotics standpoint [3].
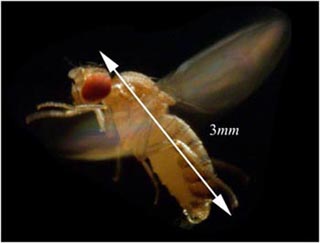
To better understand the biomechanics underlying fly flight, precise measurements of the flight forces of these tiny (3mm long) insects must be obtained. MEMS technology provides the opportunity to develop much smaller and inexpensive microforce sensors with a high sensitivity and large bandwidth. Importantly, sensor mechanical properties are well-defined, allowing novel sensor designs to be implemented. Due to their small size, MEMS-based microforce sensors can be readily integrated into existing experimental setups and, therefore, provide a significantly enhanced data acquisition technology for biomechanical research.
Flight Force Measurement Using a Single Axis MEMS Force Sensor
Figure 2 shows a schematic and an SEM picture of a single axis MEMS force sensor [4]. A differential tri-plate comb drive is constructed by separating the two stationary comb sets (1) and (3) on either side of the movable comb set (2), which is suitable for production using bulk micromachining. Microfabrication is based on deep reactive ion etching (DRIE) on silicon on insulator (SOI) wafers. The sensor has a high sensitivity (1.35mV/µN), good linearity (<4%), and a large bandwidth (7.8kHz), and is therefore well suited for characterizing flight behavior of fruit flies.
Figure 3 shows a fruit fly tethered to the force sensor probe and the force sensor wire bonded to a PCB. The measured signal is periodic, with a fundamental frequency just above 200Hz, corresponding to the typical wing beat frequency of fruit flies. The measured instantaneous lift forces are as high as 35µN, as shown in Figure 4.
The fruit fly flight force measurement results demonstrate the effectiveness of this technique for reliable and precise real-time measurements of flight forces in tethered flying fruit flies, promising important technological advance for biomechanical studies.
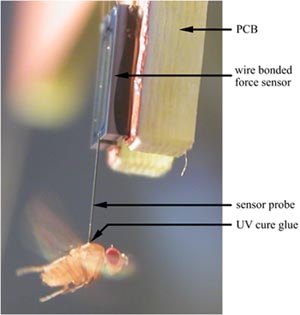
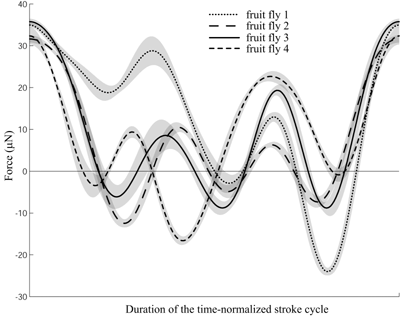