Bio-inspired Helical Swimming Microrobots
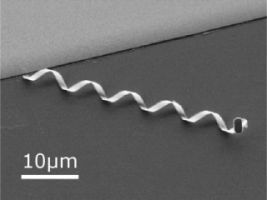
A number of robotic swimming methods have been proposed at relatively small scales. Because many of these methods rely on reciprocating motions, they do not scale downwards. Yet over three billion years ago bacteria evolved a swimming strategy at micrometer dimensions that nature has had difficulty improving upon. Just over thirty-five years ago their swimming technique using rotating flagella was first described by H.C. Berg and R.A. Anderson (Nature vol. 245, pp. 380-382, 1973). Inspired by the flagellar motion of bacteria such as Escherichia Coli (see video 6), we have recently developed artificial bacterial flagella (ABF). Our ABF represent the first demonstration of wireless swimming microrobots similar in size and geometry to natural bacterial flagella, and are many orders of magnitude smaller than existing artificial helical swimmers.
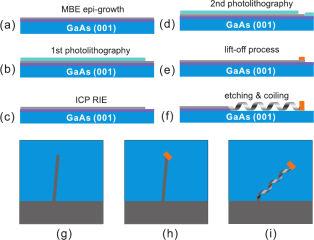
Our first generation of microrobot consists of two parts: a helical tail and a soft-magnetic metal head. The tails are 27 to 42 nm thick, less than 2um wide, and coil into diameters smaller than three microns. The fabrication of ABF is based on a self-scrolling technique. The helical tail is patterned in 2D as an InGaAs/GaAs bilayer nanoribbon or an InGaAs/GaAs/Cr trilayer nanoribbon. The metal head is fabricated from a Cr/Ni/Au thin film using a lift-off process. The 2D films detach from the GaAs wafer and self-organize to form tethered helical robots. To untether the helical swimming microrobots from the substrate, micromanipulation is performed to cut, pick, and release them in water. After that, the helical swimming microrobots are propelled and steered precisely in water by a low-strength (1-2 mT), rotating magnetic field. Details of the experimental process can be found in (APL, 94, 064107, 2009).
By adjusting the rotating speed and direction of the magnetic field, the velocity and direction of motion of the helical swimmer can be tuned in a controlled fashion. The figure below shows an example where a 74µm long helical swimmer is driven to reach a target. The average velocity is approximately 5µm/s at 470 rpm. By inverting the rotating magnetic field, the swimmer turns in the opposite direction, and the linear motion is reversed.
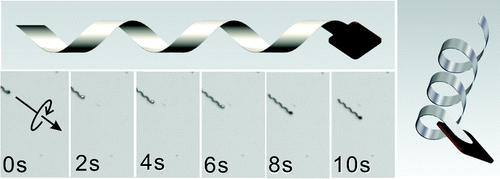
Currently, we use a 3D lithography fabrication to pattern polymer ABF's (see: Design and 3D Fabrication of Microrobotic Devices Using TPP) which are subsequently coated by a Ni/Ti bilayers to allow magnetic actuation. Arbitrary shapes can be programmed and fabricated by the 3D laser writing tool, allowing us to explore different design features.
Videos:
Video 1: 3D steering of an ABF.

Video 2: Microbead transport using an ABF.
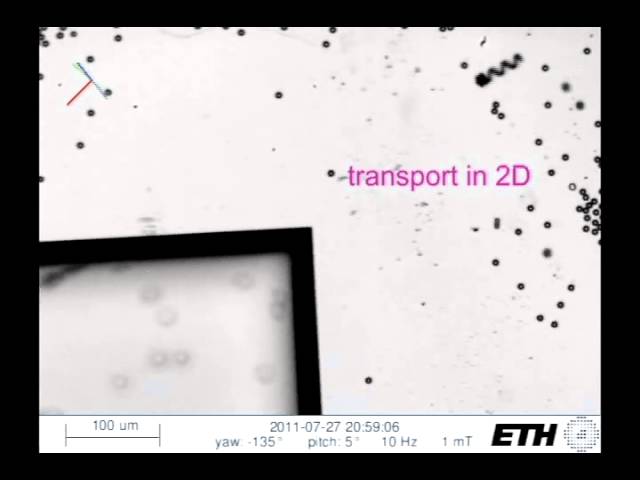
Video 3: By adjusting the rotating speed and direction of the magnetic field, velocity and direction of motion of the helical swimmer can be tuned in a controlled fashion. This video shows a helical swimming microrobot moving towards a target (black dot) in water.

Video 4: This video shows three left-handed ABF swimming forward, backward and turning.

Video 5: This video is a narrated overview of our work with helical nanobelts as motion converters that appeared in the video proceedings of the 2008 IEEE International Conference on Robotics and Automation (ICRA 2008).
